- 業務効率化
- 技術伝承
- DX
製造工場での技術伝承(継承)問題を3Dデジタル工場で解決
暗黙知と人手不足で困窮する製造現場
この工場では、50歳以上のベテランエンジニアが過半数を占め、20,30代の若手は全体の15%ほどである。敷地内に新しい工場を建てていた頃から在籍しているエンジニアは、定年を迎えて再雇用制度を活用しながら業務にあたっている。徐々に退職していくベテランエンジニアのノウハウを若手エンジニアに継承したいのだが、なかなかうまくいかない。
昨年度導入したPLANTAXIS®によって、これまでとは違う形でノウハウの伝承が進んでいる。
暗黙知と人手不足で困窮する製造現場
この工場では、50歳以上のベテランエンジニアが過半数を占め、20,30代の若手は全体の15%ほどである。敷地内に新しい工場を建てていた頃から在籍しているエンジニアは、定年を迎えて再雇用制度を活用しながら業務にあたっている。徐々に退職していくベテランエンジニアのノウハウを若手エンジニアに継承したいのだが、なかなかうまくいかない。
昨年度導入したPLANTAXIS®によって、これまでとは違う形でノウハウの伝承が進んでいる。
業務両立・コミュニケーション不足から進まない技術伝承
この工場では、保全マンの世代交代が課題として挙がっていた。最近は新工場建設やライン増設の案件は比較的減り、現状の設備をいかにうまく使うかが大切になってきた。経営方針として保全マンの数は徐々に減らす流れがあり、新卒者の数は以前と比べて大きく減っている。ベテランエンジニアは高齢化が進んでおり、保全品質の維持のため再雇用制度を活用して活躍してもらっているが、5年後はこのような体制を組めなくなる。また、人員に余裕はないため、ベテランと若手が組んで業務にあたるのも現実的ではなく、ベテランから若手への技術伝承は中々進んでいなかった。
すれ違うベテラン技術者と若手技術者
ベテランにヒアリングをすると「若手が積極的に話を聞きに来ない。何が知りたいか分からないので伝えようがない」という回答があり、若手にヒアリングをすると、「ベテランに聞くと、そんなことも分からないのかという顔をしてくる。そもそもベテランが現役のころから書類に残していないから今困っているのに、それは棚に上げる」という回答があった。両者、聞きたい・伝えたいという気持ちがあるものの、うまく噛み合っていないようだった。また、1 on 1の教育の効率の悪さも気になった。
知識や整備ノウハウをシステムに残す
そこで技術伝承のため、PLANTAXIS®を活用してベテランの知識やノウハウをシステムに残すことにした。PLANTAXIS®はメニューを自由にカスタマイズすることが出来る。通常の設備管理に加えて、技術伝承のために以下の3つの施策を実施した。
1.機器毎に、ベテランのノウハウを入力する
ベテランは、各装置について数十年のノウハウを持っている。例えば、ある装置が更新された際、その前に使われていた装置が更新された経緯や、その際に起きたトラブル、更新の際に改良した設計のポイントなど、各装置にまつわる情報をPLANTAXIS®の設備毎の基本情報に格納することにした。また、点検時のチェックポイントや装置固有のクセなども書き込んだ。ベテランも装置毎に記載していくことで、過去の情報を思い出したり、個人で持っていた情報を添付したりすることが出来た。若手は、ベテランのノウハウを確認することで、新たな気付きや特徴を考慮した保全に繋げることが出来た。
2.3Dビューアにノウハウや気づいた点マーカー貼り付ける
ベテランの持っているノウハウの中には装置に紐づかないものもあった。例えば配管や架台、防液堤に関する内容である。これらについては機器ではなく直接3Dビューア内にマーカーでポイントを示し、情報を入れることにした。例えば、なぜこの配管材質を使っているのか、防液堤のライニングが剥がれるトラブルが起きたので、特殊なライニング素材を使っている、などといった情報や、あるタンクのアウトレット配管の部分にマーカーを置き、「ここは液流により摩耗しやすく一番肉厚が薄くなりやすい」といった具体的な情報を貼り付けていった。
3.その他業務に役立つノウハウ集
これ以外にも、プロセス全体に関する内容や、装置や場所に捉われない一般的なノウハウがある。これらはノウハウ集に情報を格納していった。自由なワードによるタグ付けや検索機能を使えるので、気軽に記載していってもタグや検索で簡単に情報を見つけることが出来た。
PLANTAXIS®なら、3Dビューアにベテランのノウハウを紐づけ、まるで現場に付箋が貼ってあるかのように
これまで、なかなか進まなかった技術伝承は、PLANTAXIS®を用いることで着実に進んでいった。特に3Dビューアと紐づいた情報は分かりやすく、工事をする際は必ず3Dビューアで周辺を確認するようになった。若手エンジニアは「まるで現場に付箋が貼ってあるようで、自分では気づかないようなことも知れて嬉しい」という。新しい担当現場に配属されたエンジニアも、予め情報が蓄積されていることにより、素早く業務を立ち上げることが出来、引継ぎ時間も短縮することが出来た。今後はこれまでのトラブルについても3Dビューアに載せていき、同じトラブルが起きないように情報をアップデートしていくつもりだ。
点群データは、工場の設備管理や工事において非常に有意義で、業務の効率性を高めることができる。
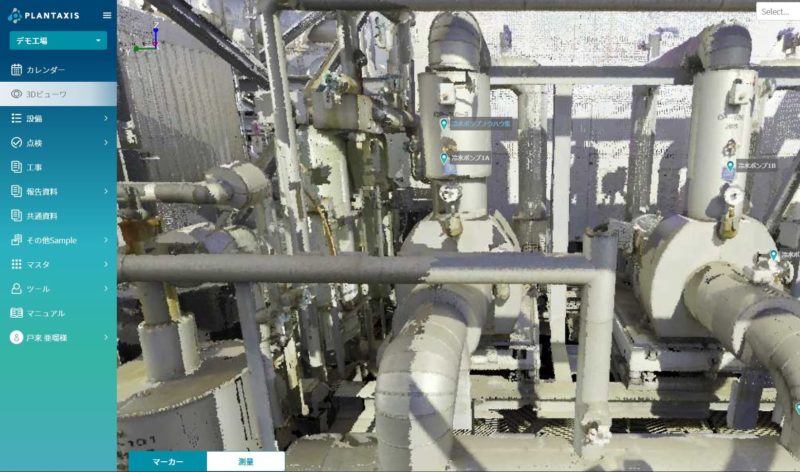
PLANTAXIS®を活用した
その他の事例
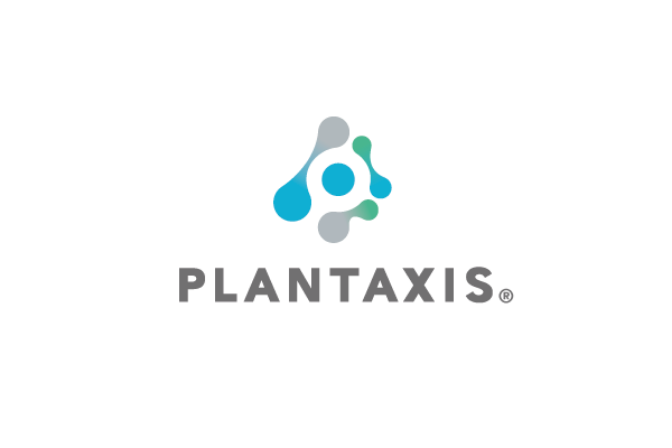
- 業務効率化
- DX
- 設備管理
製造現場の設備管理情報の一元管理・最新版管理
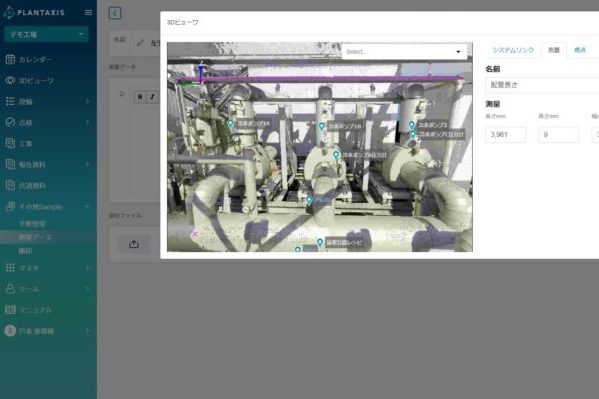
- リモート化
- 業務効率化
- 働き方改革